Waterproofing of wastewater treatment plants
Concrete structures in water treatment plants are constantly exposed to extreme conditions. Tanks, reservoirs, and channels remain in prolonged contact with corrosive or biologically active liquids, chemical agents, and continuous hydrostatic loads.
These stresses can cause infiltration, reinforcement corrosion, and structural degradation, compromising both the functionality of the structure and the quality of the surrounding water and soil.
Effective structural waterproofing is therefore essential from the design stage: cementitious mixtures should be optimized for low porosity and integrated with complete barrier systems to ensure a watertight seal, extend the service life of the structures, and reduce long-term maintenance costs.
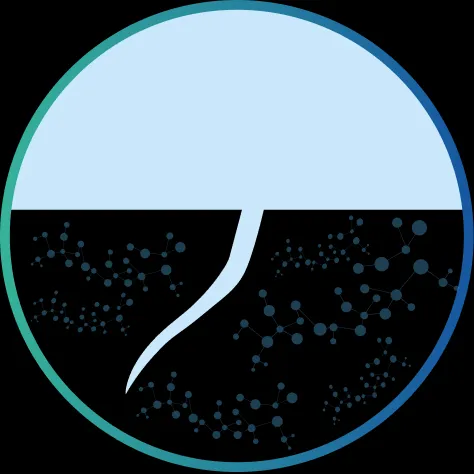
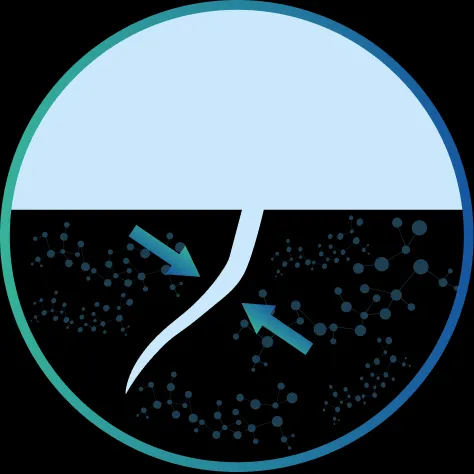
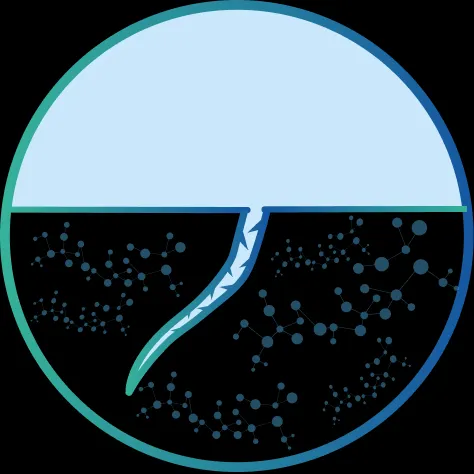
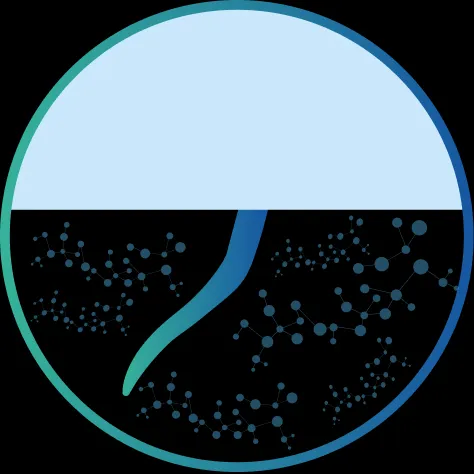
concrete
Critical issues of water treatment structures
The operating conditions of wastewater treatment plants pose numerous challenges to reinforced concrete. In particular:
- Water infiltration and permanent humidity: stagnant water or water under static pressure promotes oxidation of the reinforcement and leaching of the concrete.
- Aggressive chemical attacks: acids, chlorides, sulfates, carbon dioxide, and other agents reduce the internal pH of the concrete, causing carbonation and accelerated corrosion of the reinforcement.
- Freeze/thaw cycles: in cold climates, water trapped in the microcracks of the concrete expands when it freezes, generating recurrent cracking with each cycle.
- Mechanical stresses and hydrostatic pressures: structural loads, vibrations, or ground movements introduce stresses and cracks that can facilitate new infiltration.
These factors damage the concrete. Uncontrolled infiltration causes corrosion of the reinforcement. Furthermore, they can lead to chemical attack of the materials.
This causes cracks and reduces the section. Finally, it decreases the load-bearing capacity.
Any compromise of the seal also promotes contamination of aquifers and soil, underscoring the importance of protecting treatment structures from the outset.
Requirements for structural and durable waterproofing
In wastewater treatment plants, a structural and integral waterproofing approach is necessary. From the pouring phase, low-porosity cementitious conglomerates should be used, possibly with crystallizing agents, to minimize the passage of water and harmful solutes.
It is also necessary to create a continuous barrier on the surfaces and, above all, on the construction joints (with hydro-expansive sealants, tapes, or waterstop profiles) to ensure that every structural discontinuity is waterproofed.
In this way, an impermeable and self-healing cementitious mass is obtained from the first pour, capable of withstanding hydrostatic load cycles, thermal variations, and chemical attack without deteriorating. A hermetic seal designed in this way effectively prevents infiltration, protects water quality, and extends the life of the plant.
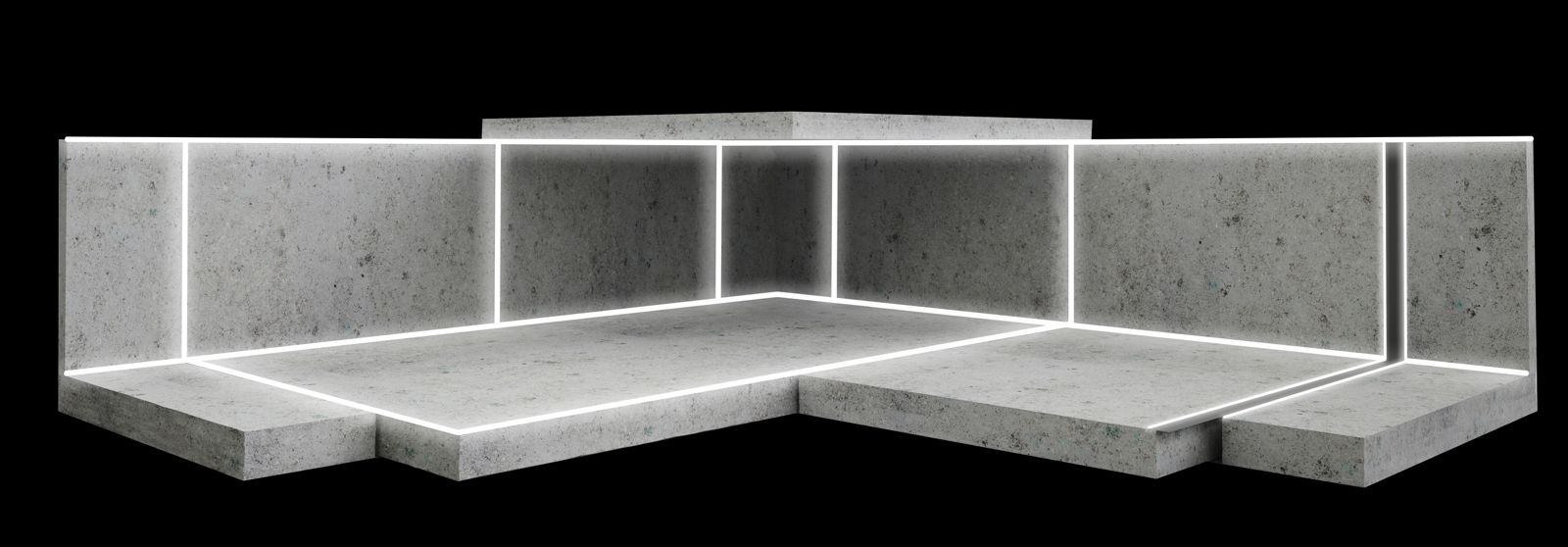
Combined solutions: crystallizing additives, membranes, and joint systems
Drykos promotes an integrated approach that combines different complementary technologies for maximum concrete protection. In particular, the ideal system includes:
- Crystallizing additives in the mix: liquid binders mixed with the concrete (e.g., Drymix Ultra) that react with the cement hydrates, forming insoluble microcrystals in the pores. These crystals progressively occlude the capillaries, making the entire cementitious volume impermeable from the inside and giving the material a self-healing action in the presence of residual moisture.
- Special membranes and sheets: for example, bentonite geotextiles or polymeric sheets applied to the walls or in casting reprises. These films offer an additional hydro-reactive barrier that is activated upon contact with water, automatically repairing any critical points on the surface.
- Elastomeric sealants and injection mortars: polymeric or cement-based products to be applied on-site for targeted treatments of cracks or localized defects. They ensure immediate sealing of construction joints and rapid intervention on any damage found during construction or on existing structures.
- Waterstop profiles (PVC or hydro-expansive rubber): inserted in structural joints to ensure continuity of the waterproof barrier and effectively manage hydrostatic pressures. These profiles expand upon contact with water, sealing the joints between concrete elements.
These components operate in synergy: crystallizing admixtures waterproof the internal mass of the concrete, while membranes, sealants, and waterstops guarantee sealing on surfaces and in joints. The result is a structure that is waterproofed in depth, resistant to surface attacks, and durable over time.
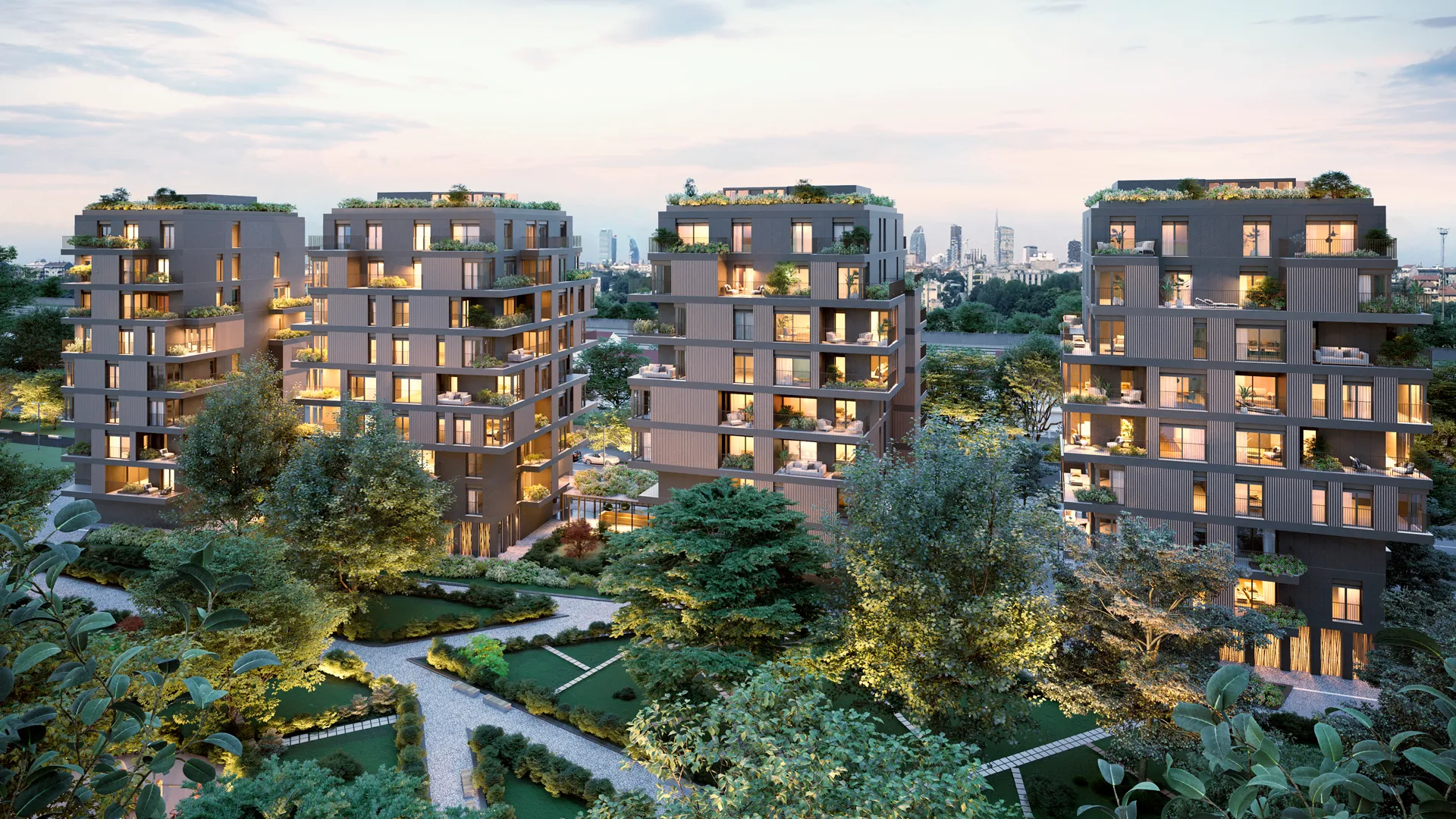
DRYBOXSYSTEM®: distinctive characteristics
DRYBOXSYSTEM® by Drykos represents an integrated, turnkey system for the protection of new concrete structures. Its main features include:
- Active and self-healing waterproofing: the crystallizing admixture incorporated into the concrete mix reacts with water to form a network of insoluble microcrystals that seal the pores. In the event of micro-cracks forming (up to 0.5 mm), the crystals reactivate autonomously, “sealing” the water pathways without external intervention.
- Complete and compatible system: each component (admixtures, membranes, sealants, waterstop profiles) is designed to be compatible with the others, ensuring a continuous barrier and a uniform distribution of waterproof performance throughout the structure. The integrated design of the system ensures total hermetic sealing of the structure from the analysis phase through to on-site application.
- Advanced chemical resistance: concrete treated with DRYBOXSYSTEM® becomes substantially resistant to aggressive substances (bacteria, organic acids, salts, detergents, etc.), preventing chemical degradation of the cementitious materials. This is crucial in purification plants, where the matrix can be exposed to biologically active effluents and hazardous chemical agents.
- Durability over time and reduced maintenance: thanks to the permanent waterproofing of the concrete mass from the time of pouring, the structure maintains its performance unchanged over time. Unlike traditional coatings, which deteriorate and require reapplication, the Drybox system does not require continuous extraordinary maintenance. In practice, this translates into fewer repair and restoration interventions, lower operating costs, and water savings thanks to the elimination of leaks.
- Regulatory compliance and sustainability: the components used are certified for contact with drinking water and are VOC-free. The system is designed to meet the highest environmental standards (LEED, SDG, green building). In particular, the adoption of DRYBOXSYSTEM® helps to drastically reduce the ecological footprint of concrete structures – up to 65% according to internal studies – thanks to the lower production of waste and emissions, preserving water resources and soil.
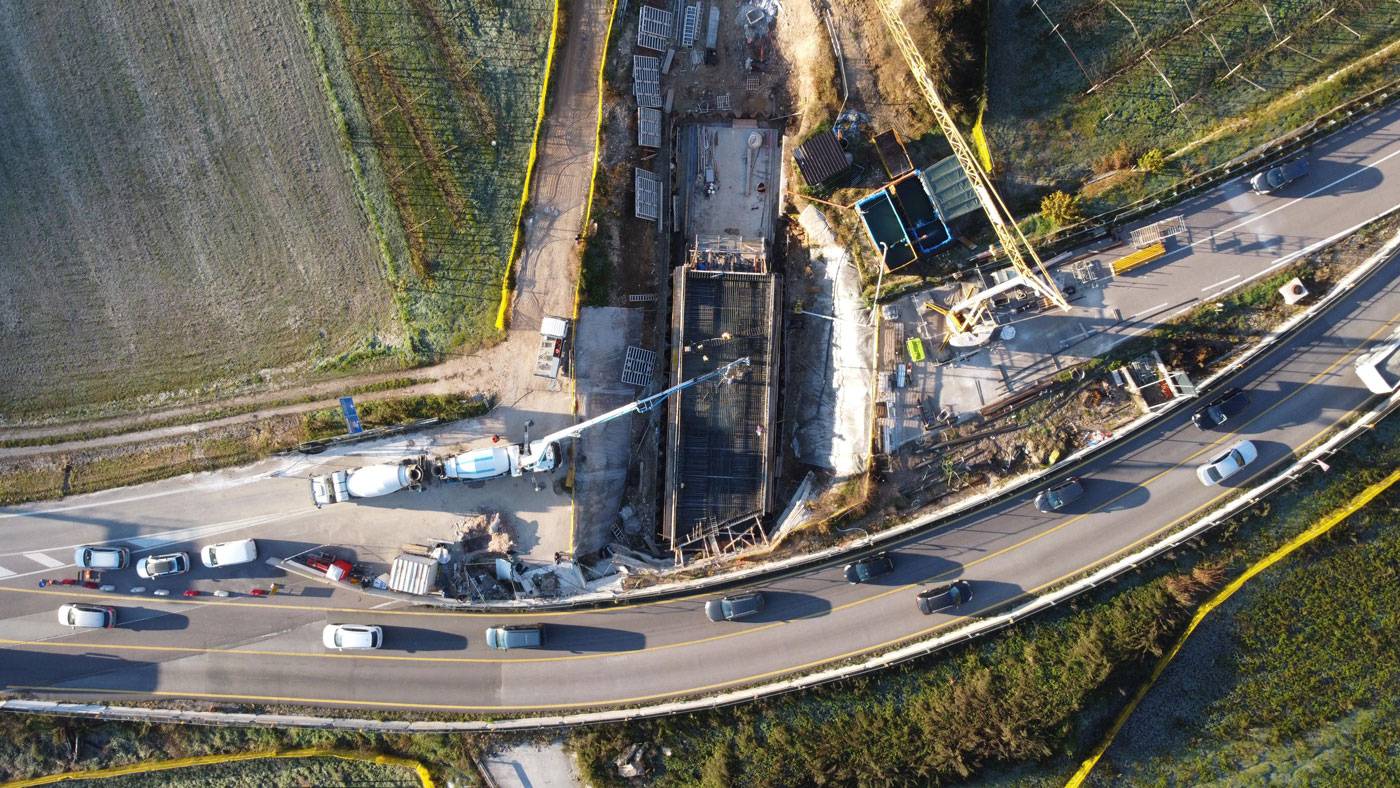
Practical applications and environmental benefits
DRYBOXSYSTEM® is successfully used in all cases where it is essential to avoid any infiltration. Typical applications include storm water storage tanks, underground tanks for drinking water, fire-fighting tanks, wastewater and digester treatment plants, as well as industrial containment tanks (chemical, oil, energy sectors).
Thanks to the complete protection offered by the system, these structures remain waterproof and safe: the absence of leaks preserves water resources, prevents contamination of aquifers and land, and protects the surrounding ecosystem.
In terms of sustainability, the use of the Drybox system promotes the achievement of ambitious environmental and regulatory objectives. Eliminating infiltration reduces water waste and the treatments required for wastewater, while the use of recyclable crystalline materials without VOC solvents contributes to compliance with green building directives.
Overall, crystallizing technology can achieve up to 65% less overall environmental impact compared to conventional solutions. The result is a safer, more durable, and “green” structure, compliant with the requirements of industry regulations and sustainability certifications.
In summary, DRYBOXSYSTEM® offers designers, construction companies, and public bodies an advanced and proven solution to guarantee waterproofing, durability, and chemical resistance to purification plants. Thanks to permanent waterproofing and a sustainable approach, this system helps to extend the useful life of structures while respecting the environment.
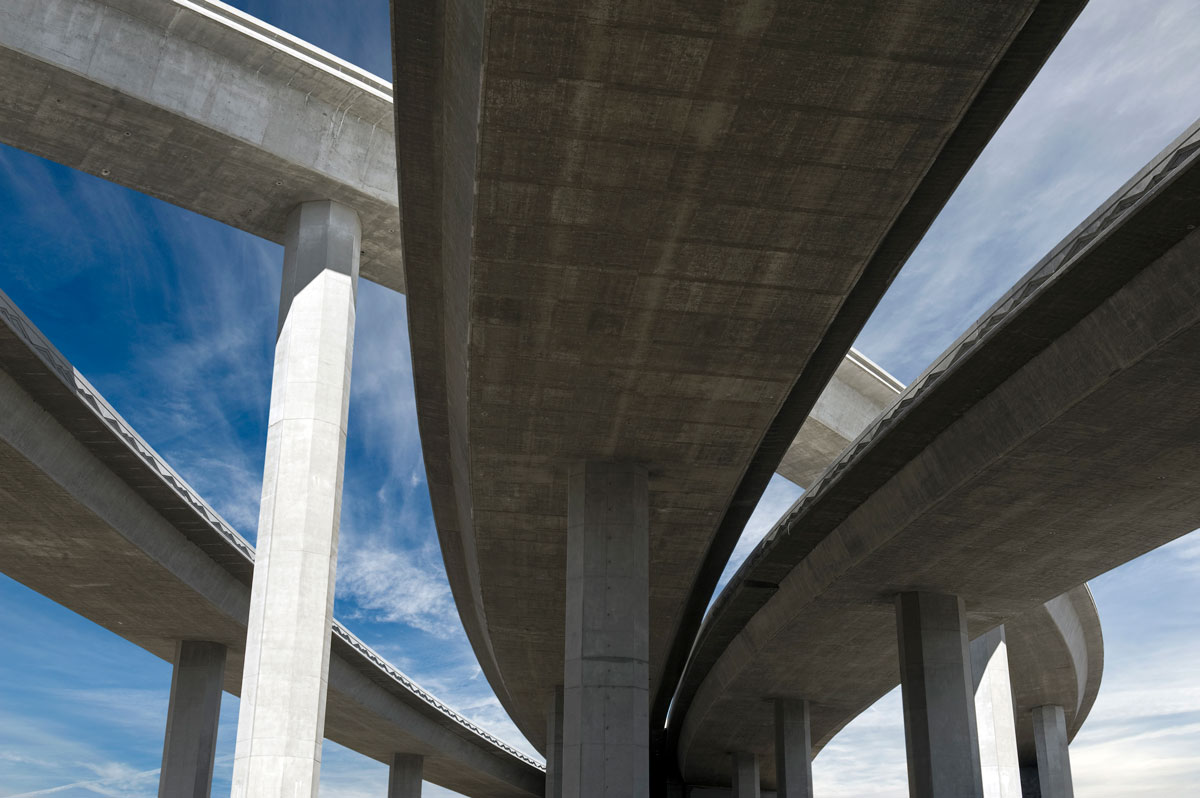
MLN
waterproofed
%
%
footprint
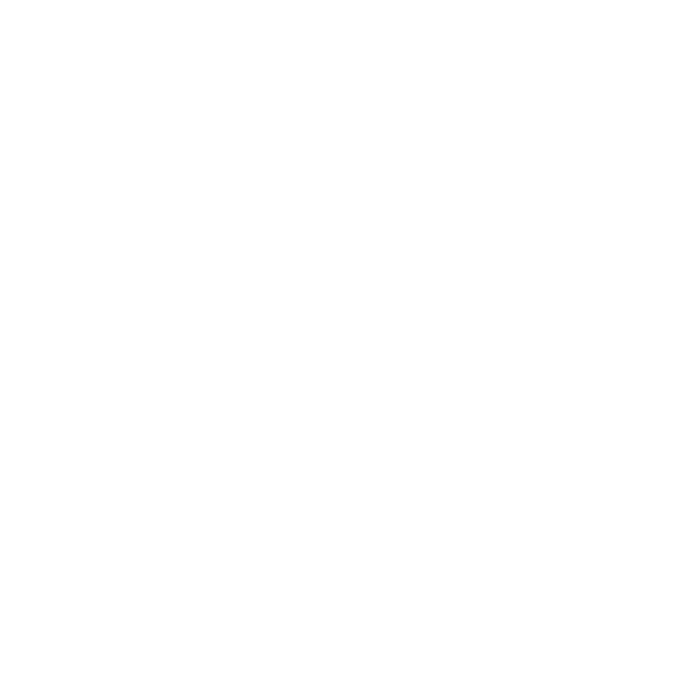
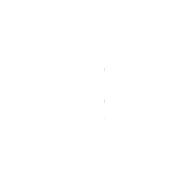
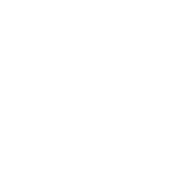
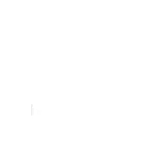
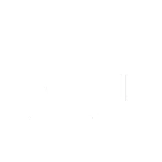

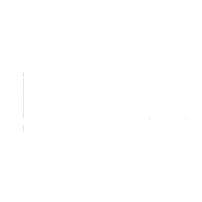
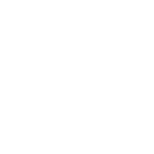
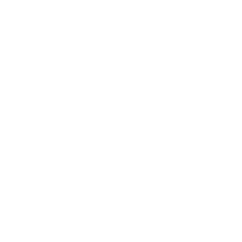
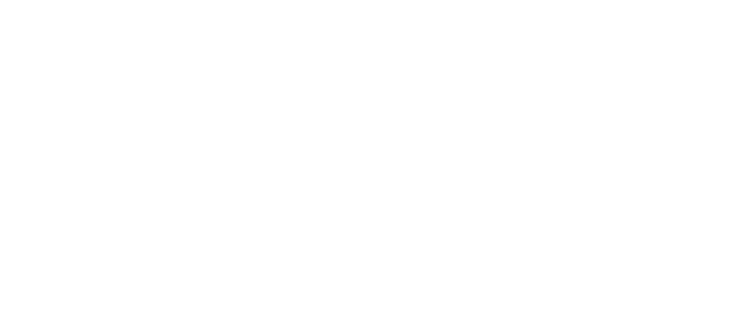
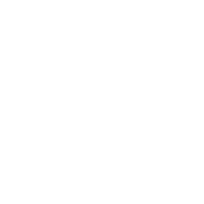
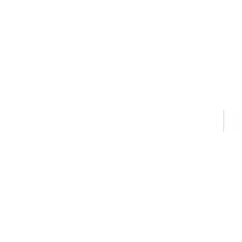
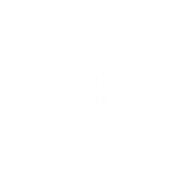
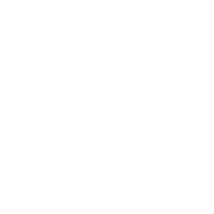
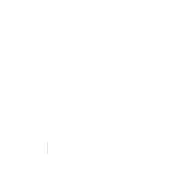